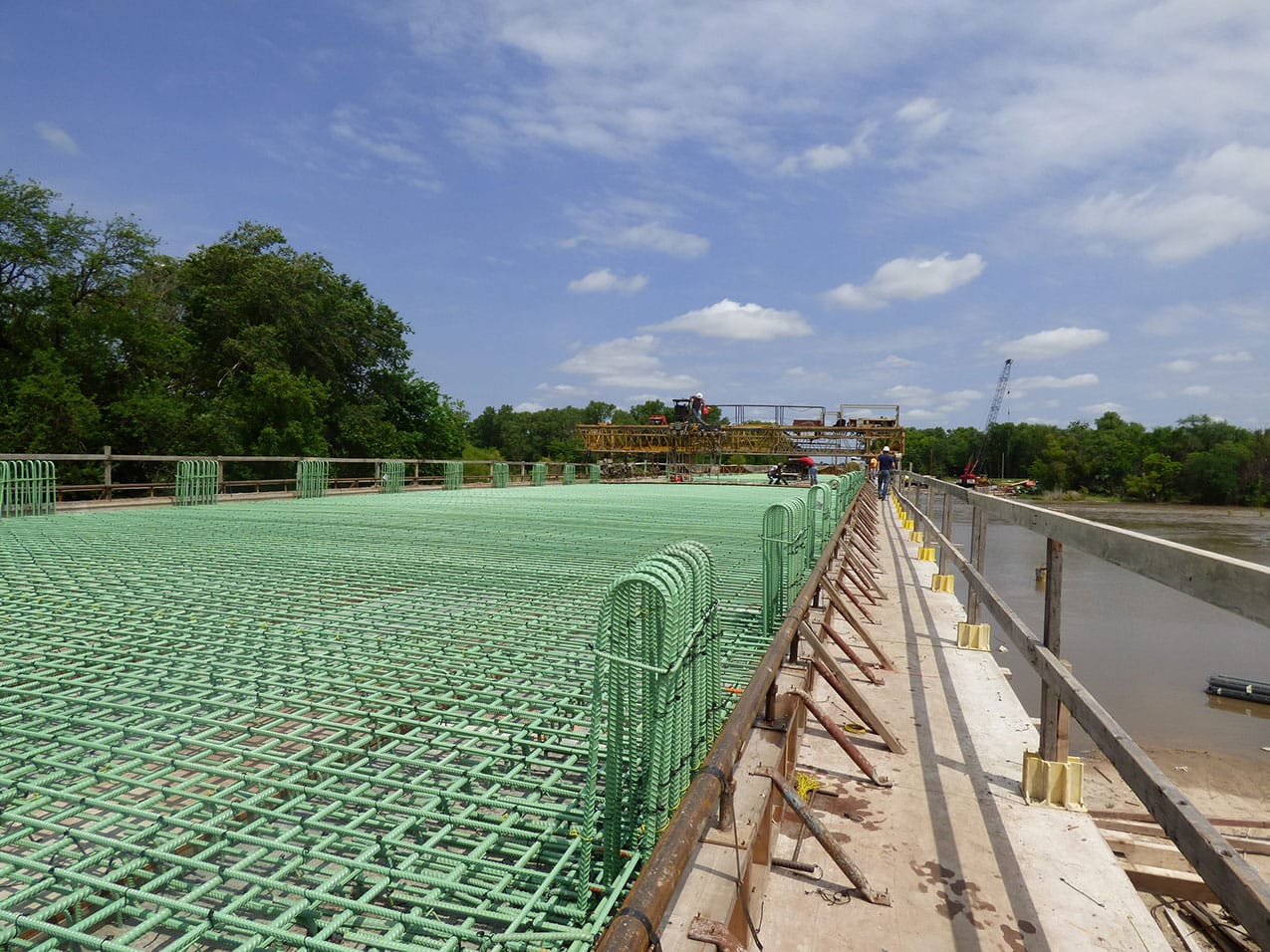
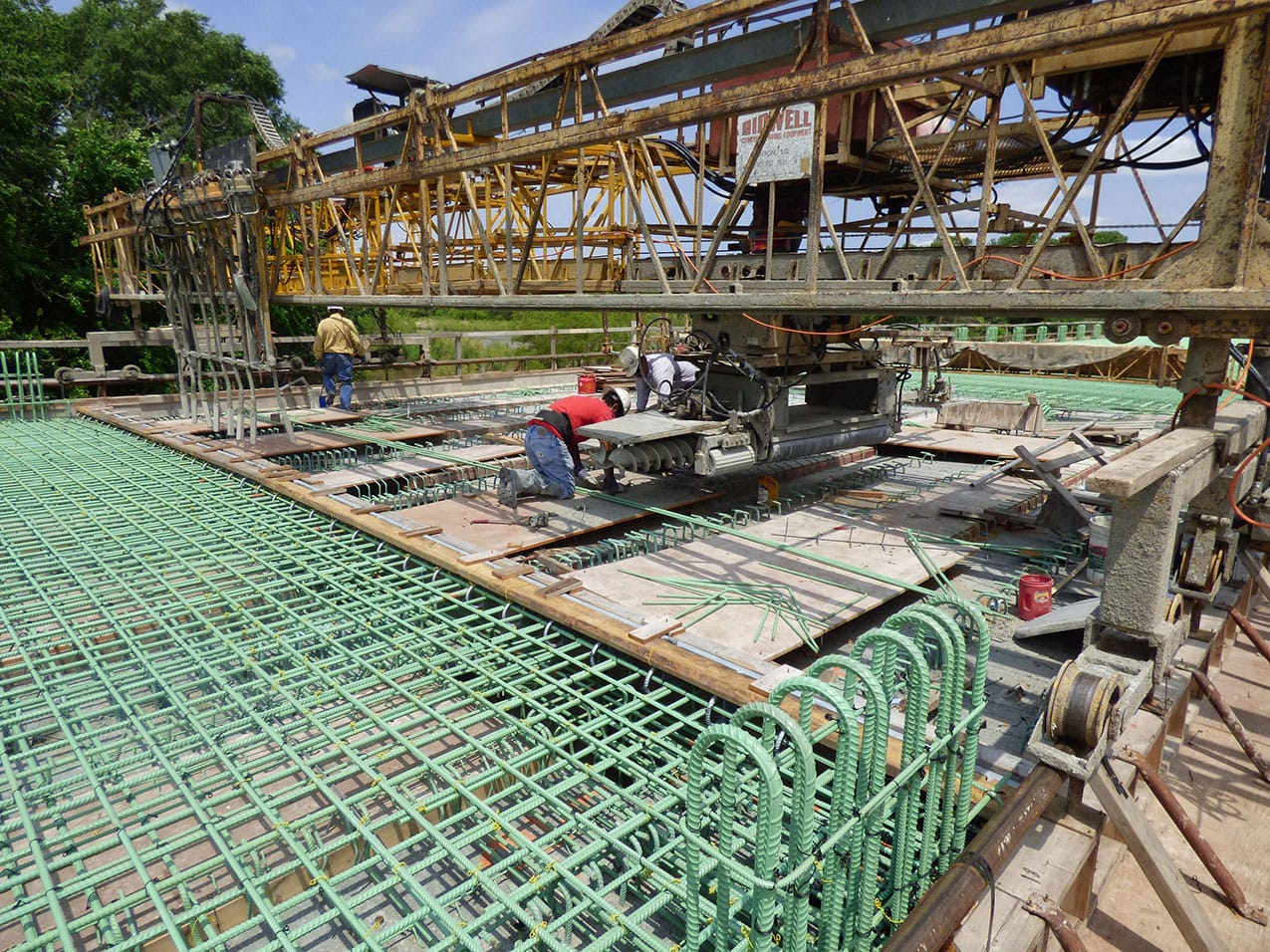
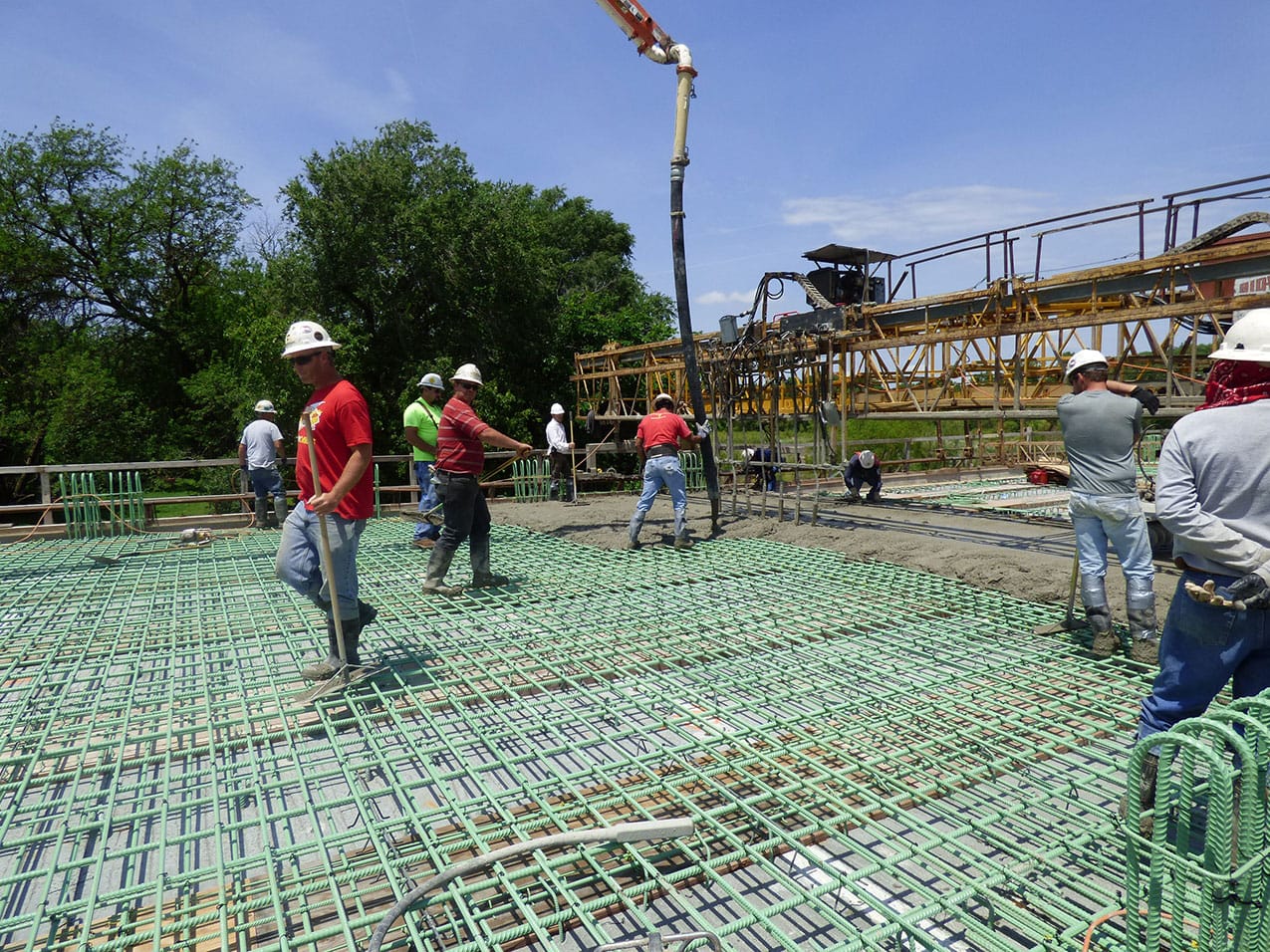
MOUNT HOPE BRIDGE
Mount Hope, KS
PROJECT DETAILS
- Design Criteria: 683-foot-long, 38-foot wide, 6-span (110-115-115-115-115-110) precast, prestressed concrete bulb-tee girders and cast-in-place concrete deck, pier caps, columns, and abutments with pile foundations.
- Owner: Sedgwick County Public Works, Wichita, KS
- Designer: WSP, Wichita, KS
- Builder(s):Dondlinger Construction, Wichita, KS
- Precaster: Coreslab Structures, Kansas City, KS
Following 60 years of service to the Mount Hope, Kansas, community, local officials determined that their bridge spanning the Arkansas River needed to be replaced, both due to deterioration and to accommodate higher traffic demand. The replacement design, 12 feet wider, features a superstructure of precast, prestressed concrete beams reinforced with epoxy-coated rebar.
The original eight-span, 654-foot-long steel bridge provided key access along 279th Street West. But at 26 feet wide, it also created a bottleneck the local farming community needed alleviated. To resolve these issues, engineers at WSP, a global engineering and professional services consultancy, replaced it with a six-span, 38-foot-wide bridge. In part, this design was selected due to the fast timeline required to minimize the closure period for the vital route and to keep construction out of the wetted channel from April to August to protect endangered fish species.
The project was completed several weeks ahead of schedule, noted Abdul Hamada, a project manager with WSP, in an article on the project for the Spring 2018 issue of Aspire magazine. “Sedgwick County Public Works provided a temporary construction staging area for the contractor, and all environmental and hydraulic permits were acquired before the start of construction,” he wrote. “The simplicity of the plans and the use of the shallow precast concrete beams were major factors in completing the project ahead of the tight schedule.”
The six spans (110-115-115-115-115-110 feet) were topped by an 81/2-in.-thick cast-in-place concrete deck. Cast-in-place pier caps, columns, and abutments with pile foundations also were used.
Epoxy-coated reinforcement was used in the abutments, girders, deck, and railings, Hamada told EIG. “It is typical to use epoxy steel for all KDOT and local-agency bridges in Kansas,” he notes. “The epoxy coating will add another layer of protection to the reinforcing steel. We have been specifying epoxy-coated reinforcing steel for the past three decades in Kanas.”
Officials consider epoxy coating to be critical to ensuring a long service life to the structures. “Epoxy will provide protection of the reinforcing steel in concrete from rusting, deterioration, and section loss of material,” he says. “It will also lengthen the life of the structure and keep the concrete from spalling.” The typical specification is for ASTM A615, grade 60 reinforcing steel, he notes.
To add to the structure’s longevity, three-column, cast-in-place concrete piers were constructed atop a concrete foundation supported by friction-steel piles. The number of pier bents in the channel was decreased, and the piers were aligned with the flow of the channel to minimize impact of any potential scour.
A 5-foot-deep web wall was added below the pier beam and between columns to eliminate the accumulation of any debris or brush that could get tangled between piers, again to mitigate possible causes for scour.
The bridge lies in a high-risk Federal Emergency Management Agency (FEMA) flood zone, called AE, which has a 1% annual chance of flooding, more commonly known as the “100-year floodplain.” Bridges in a FEMA zone AE must be designed to prevent any rise to the backwater surface profile.
As a result, the new waterway opening needed to match the existing opening to keep flow characteristics and conveyance of the river unchanged. This hydraulic issue was resolved by the careful placement of abutments, piers, and superstructure. The project successfully achieved minimal impact the channel below ordinary high water.
The selection of superstructure type was a key decision for this bridge project because it related to the environmental concerns, construction costs, and maintenance costs, Hamada wrote. Low-profile precast, prestressed concrete bulb-tee girders maximized the span lengths and allowed fewer bents in the Arkansas River. These NU1100+25 Nebraska girders, both 110 and 115 feet long, were 3′ 85/16” deep, providing a 30:1 span-to-depth ratio.
The NU1100+25 girders had a top flange approximately 4 feet wide and a bottom flange approximately 3′ 3″ wide containing 0.6-inch-diameter prestressing strands. “Precast, prestressed concrete girders with wide flanges were chosen in part because they would take the least time for construction over the wetted channel, which helped the project deal with the scheduling limitations related to protection of endangered fish species,” Hamada wrote.
Another reason that shallow bulb-tee girders were chosen was to minimize the raising of the vertical profile grade of the road, he wrote. “Keeping the profile low and keeping construction away from a nearby intersection minimized both right-of-way acquisition and approach work. This strategy, in turn, limited the impact of the project on adjacent property owners and reduced the cost of the project significantly.” The precast, prestressed concrete girders were also chosen because of their low maintenance costs.